-
GuillermoExcellent! Fast delivery! I like to work with you again!
-
Perus ColetteIt is my pleasure to do the business with LiFong,they always do the best for us.
-
Robin SeifertI like the products and service provided by LiFong. They really take our interest into consideration.
-
SjakThat's true we enjoy doing business with you.
-
Kelly MarshLiFong is one of our desired vendors in China
-
Raimund SchenkProduct Quality, Competitve Prices, always one of our key suppliers
Customized Aluminium Die Castings Product Powder Spraying For Machinery
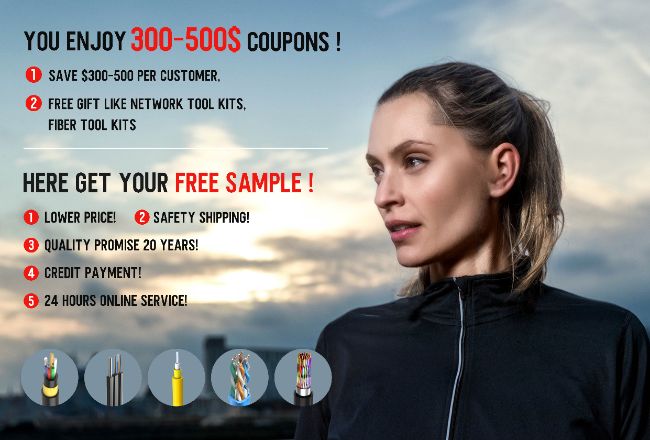
Contact me for free samples and coupons.
Whatsapp:0086 18588475571
Wechat: 0086 18588475571
Skype: sales10@aixton.com
If you have any concern, we provide 24-hour online help.
xMaterial | Aluminum | ODM | YES |
---|---|---|---|
OEM | YES | Application | Machine |
Surface Treatment | Powder Spraying | Craft | Die Casting |
Highlight | aluminium die casting process,high pressure die casting |
Quick details:
Precision copper pipe heatsink
Large image: aluminum fin heat sink with copper pipe
Materials: pure copper C1100 strips, purity over 99.5%
Big power copper pipe embodied aluminum Fin heat sink for floodlight and stage lamp
According to customer's requirements
Large image:
Aluminum fin heatsink with copper pipe
300W big power copper pipe heatsink
Copper pipe heatsink for stage lamp
Heatsink with copper pipe for stage lamp
Applications:
Stage lamp
Specifications:
Overall dimensions: 256*240*103mm
Fin dimension: 220mm diameter
Aluminum fin thickness: 0.5mm
Fin quantity per row: 20 pieces
Copper tube: 8mm diameter
Copper tube quantity: 8 pieces
Aluminum bottom board thickness: 7mm
Tube quantity: 6 pieces
Part weight: 1.9kg
Materials:
Pure copper C1100 strips, purity over 99.5% (standard: JIS H3250-2006), pure aluminum board A1060, purity over 99.6%, (standard: GB/T3880-2006)
Less impurity brings very good electrical and heat conduction
Excellent performance in corrosion-resistant too
Processing techniques:
1. Aluminum fins: progressive die stamping
2. Copper board: extrusion + CNC machining
3. Copper tube forming: automatic tube bending + burn into tip ends
4. Aluminum board and enclosure nickel-plated, copper fin passivity (insulation, oxidation and corrosion resistance)
5. Assembly: automatic fin wearing/assembly, then fixed by overflow soldering and screw/rivet combination
6. Quality check
7. Packing
Advantages:
1. Professional research and design team, strong and automatic equipment: progressive stamping, automatic tube bending machine, automatic fin wearing machining
2. Strict quality control in each process and finish product quality control
3. Short delivery lead-time: 15-30 days
4. OEM or ODM (optional)
5. Comprehensive after-sale service, quick responses for daily communication